How Jersey Barriers Got Their Name: The Birth and Evolution of Today’s Highway Barricades
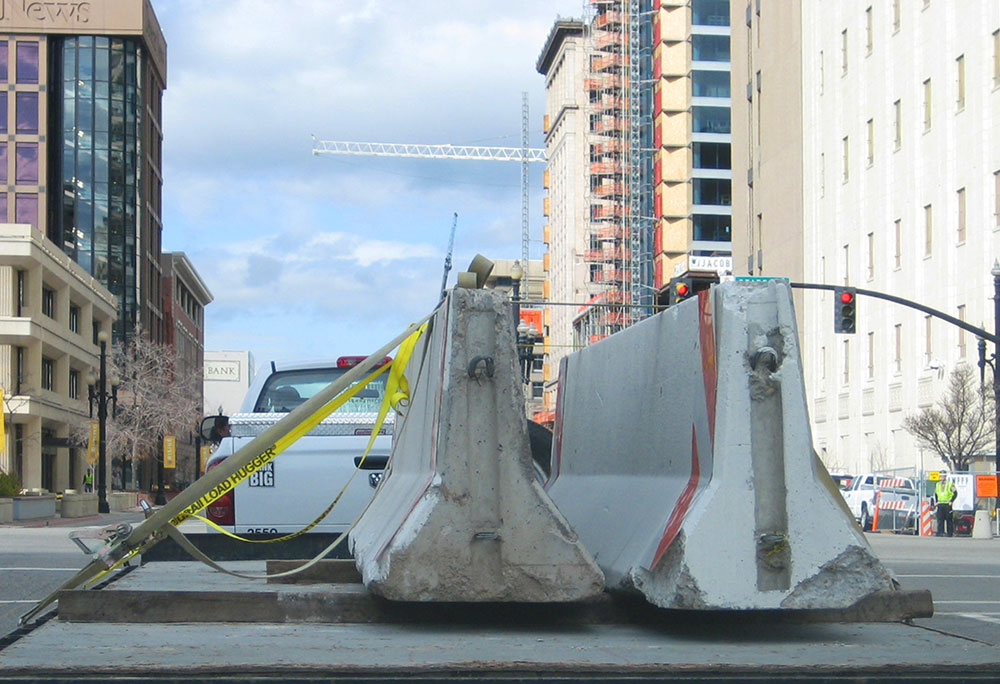
New Jersey is known for a lot of things: beautiful shorelines, strong accents, and — whether you like it or not — not being able to pump your own gas. It is also where Jersey Barriers come from. You may not realize it, but you see them all the time.
The Jersey Barrier — also known as a Jersey Curb, K-rail, or Jersey Wall — refers to the barricades you see along the center and sides of highways, at construction sites, in parking lots, and pretty much anywhere traffic is being directed. They are often made of concrete, especially for permanent installations, but are also seen as the more portable bright orange and white plastic versions that are filled with sand or water.
Who needs ‘em?! Oh, right— we do.
Before the 1940’s, barricades like this didn’t really exist, but as more cars made their way onto the burgeoning highway system, better dividers became necessary. There was a particularly treacherous stretch of California’s US-99 called the “Grapevine Grade,” known for its terrifying curves and steep grades. Unsurprisingly, this part of the highway had some of the highest numbers of fatal head-on collisions, so the California Division of Highways decided to experiment with the first “parabolic concrete barriers.”
Hitting you with a Geometry Fact! “Parabolic” (a fancy math word for “U-shaped”) refers to the concave sides of the barriers, having a shallower angle towards the bottom, and a more vertical angle higher up — the shape you’d get if two letter U’s body slammed some concrete between them. Pretty much any barricade in this shape is now known in the ‘biz as a “Jersey Barrier”.
The advantage of this shape is that instead of simply stopping a vehicle from crossing the median, the tire of the car or truck rolls over the lower angle towards the bottom and is redirected by the increased higher angle back onto the road, avoiding collisions and minimizing vehicle damage.
Jersey Barriers are born
Following in California’s footsteps, New Jersey decided to try out some concrete barriers of their own in 1955. They were installed in a particularly dangerous, mountainous section of US-22.
Fun Fact! The first Jersey Barrier was just 18 inches tall!
😮 so tiny!
After the initial success of these barriers, changes were made through a process of trial and error (not the recommended strategy today), observing results where these barriers were placed. The barriers grew out of their 18-inch infancy into a 20-inch toddler version, which was installed along almost 75 miles of highway. These proved not quite tall enough to ride along the big-boy roads, with some vehicles still able to clear them, so they grew to a gawky middle stage of 24 inches high. By 1959 New Jersey settled on the all-grown-up standard of 32 inches high with a 24-inch base. This version met all Federal safety standards, and is still the most widely used today.
Let’s talk numbers
Once New Jersey settled on their barrier dimensions and slopes, a standard was set. Other states, however, had questions about cost and actual safety improvements (they weren’t so keen on the trial-and-error method). They would want some cold, hard numbers before they doled out the cold, hard cash to put in these barriers.
Throughout the 1960’s, New Jersey and California conducted a series of crash tests with the Jersey Barrier, concluding that it was both effective and low-maintenance. Both factors contributed to widespread adoption of highway barriers.
As more states began to use the Jersey Barrier, it became more modular, being poured into molds and later connected into a wall, rather than poured in place on-site. This lowered the cost, which was music to America’s ears. By 1972, California itself then installed Jersey Barriers along 132 miles of its highway, and other states followed suit.
Why change when you’ve got a good thing going?
As time passes, traffic, road technology, and vehicles all change as well. The Jersey Barrier has gone through a lot of changes to get to the shape we know today, but it still continues to develop.
Some states, including New York, Massachusetts, and New Jersey itself have adopted the taller, 42-inch version, also (very creatively) called the Ontario Tall-Wall. These higher barriers help block distracting headlights from oncoming traffic, and are safer for large trucks. Another version, the F-shape barrier has a flatter slope and has a lower bottom section to compensate for more modern cars.
Fun? Maybe. Fact? Yes! It is referred to as F-shape not because it’s shaped like an F (it’s still the good ol’ Jersey Barrier shape), but because in a series of Federal Highway Administration crash safety tests, they alphabetized each version, and this variation was version F. (Today’s fact has been brought to you by the letter F).
Other minor changes include additions such as steel rebar loops in this top so they can be lifted more easily, or notches on the bottom for forklifts.
Jersey Barriers for all
One of the most notable steps in the evolution of temporary Jersey Barriers has been the introduction of plastic as an alternative to concrete. Plastic Jersey Barriers use the same concept of molding but use a heavy duty plastic shell and empty interior cavity to make the barricades light or heavy depending on which stage of use they’re in. Barricades being delivered on a truck are light! Barricades on the ground filled with water are heavy. Plastic can’t always substitute for concrete but in the right situations it can have great advantages:
- Portability – Plastic barriers are easy to set up and move around. They’re also easy to stack and palletize which makes storing and transporting them simpler and cost-effective.
- Visibility – Plastic barriers in construction zones are typically manufactured using bright orange and/or white plastic, making them highly visible.
- Clear Delineation – Interlocking barriers that form a continuous line are easy for motorists to spot and react to accordingly. Widely spaced traffic cones or barrels can be more difficult to see and may inadvertently cause accidents instead of preventing them. Plus, nothing says “I’ve got style” like a bright orange and white reflective surface.
- Versatility – As needs and uses expand, modern Jersey Barriers come with a variety of additional features. Plastic barriers can be made to easily interlock to fit different spaces, or accommodate curves. Fence panels can be added to the top of plastic barriers, contributing to site protection in construction areas. Added screens on these panels add privacy, site beautification, and marketing opportunities with branded signage.
When you need it most — the Jersey Barrier is there
Other barrier designs have come and gone, but none have been able to unseat the Jersey Barrier, and with its ever-increasing safety and versatility, it’s unlikely to be leaving anytime soon. Long shall it reign.
OTW remains at the forefront of emerging safety standards and technology. Not only do we produce jersey style barricades that emulate the iconic shape, we are consistently finding ways to improve designs and manufacturing techniques.
Just released – a 32” LCD that meets the requirements of most work sites without the bulk of a larger barricade.
At OTW Safety, we don’t just sell plastic barriers –– we manufacture them. As the designer, manufacturer and seller, we strive to provide our clients with the best products, the best service and the best value on the market. Contact us here for more information.