Learn With Us: Rotational Molding
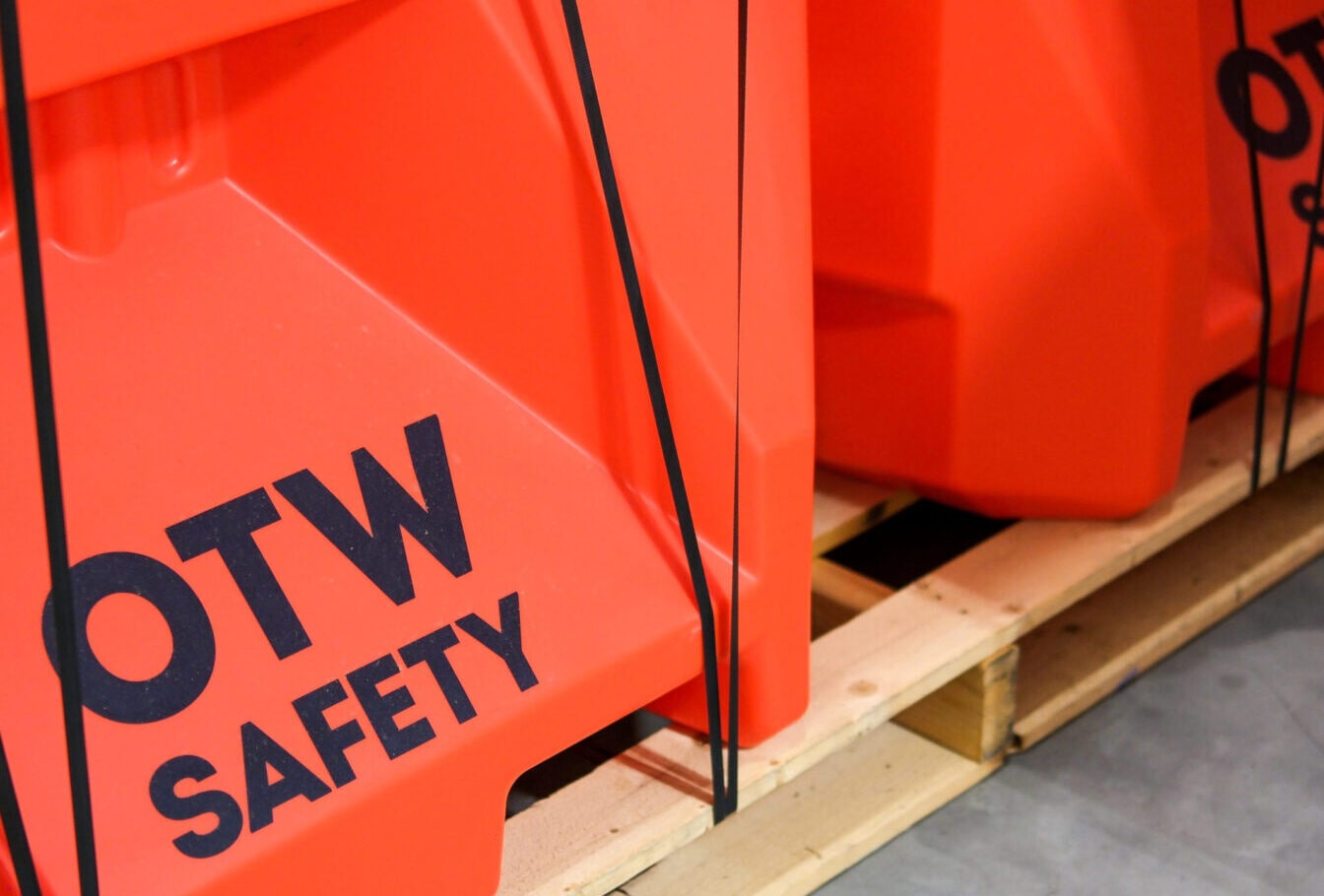
What is rotational molding?
Funny you might ask! Just a few weeks ago, we walked our team through the experience using our new rotomold, from start to finish.
Rotational molding has long been known by numerous names. According to RotoMold USA, “rotational molding, rotomolding, rotomold or rotocasting is a production process to form hollow parts of limitless size”.
To do this, first, a mold is created of the necessary part. The mold is then attached to the manufacturing machine, plastic (or powder resin, as various additives can also be incorporated, including fiberglass) is added, and the mold is slowly rotated, both vertically and horizontally, while being heated. This slow and steady process ensures that the plastic is evenly distributed, forming one cohesive piece with no seams. This process does favor the corners, which means that, while the entire piece is uniform in thickness, the corners receive slightly more material in the turning process; this gives those corners the ability to absorb shock and impact better in the places where plastic pieces generally get bumped the most.
How does rotational molding compare to blow molding?
Blow molding, on the other hand, is akin to glassblowing – it uses the properties of classic glassblowing to create hollow objects. The properties are very similar, as hot air is blown across both the glass and plastic to create said hollow objects. Blow molding can use nearly any type of plastic, such as polyethylene, polypropylene, polystyrene, PVC, or PET (most common in plastic bottled water).
First, the plastic is heated and formed into a parison (a thermoplastic hollow tube) in most cases. The parison is secured to the mold and hot air is blown across or onto the mold, redistributing the plastic throughout the interior of the cavity. This creates your hollow object, such as a bottle, or some of our very own barricades.
Like rotational molding, blow molding uses liquid plastic poured into a mold; however, as mentioned above, rotomolding uses a mold that is rotated vertically and horizontally, evenly distributing the liquid plastic. The processes are similar and create related products, but, with rotational molding, the layers of plastic or powder fuse so completely that you are left with one sturdy, seamless product. While blow molding does often give you near seamless products, and the parison can be created with varying wall thicknesses in order to change the final outcome of the product, rotational molding does it all in one smooth step.
Why did OTW invest in a rotational mold?
The 32” JSS and 42” JSS barricades are our very first rotomolded products! This is newer territory for us, but we are thrilled to be able to continue to create two of our most sought-after products right at home. This allows for precise handling and more customization for the consumer! We can create both JSS barricades in custom colors, making these safety giants visible and beautiful. Having our own mold also allows us to create permanent branding from within the mold, as opposed to a decal, if the customer desires.
Due to supply chain shortages causing delays over the past few years, purchasing our own mold allowed us to meet our customers’ demands for this critical product more easily! As we now manufacture both our JSS barricades in-house, we are able to fulfill orders of any size in a timely manner… without forcing our dedicated customers to deal with supply chain shortage issues.
It’s all thanks to you!
We take investing in our customers and partners seriously, so continuing to develop and build trust with you is one of our main priorities as we move forward with in-house manufacturing. We are honored when an individual, business, or airport chooses to partner with us in creating safe spaces. We have spent the last 30 years dedicated to that endeavor and we will spend the coming decades continuing to prioritize safety and designing, manufacturing, and providing excellent products that keep your people safe.
GIve us a call at (801)363-7740 to learn more about our rotationally molded barricades.